Market Trends of Europe Automotive Thermoplastic Polymer Composites Industry
This section covers the major market trends shaping the Europe Automotive Thermoplastic Polymer Composites Market according to our research experts:
Glass Mat Thermoplastic (GMT) is Expected to Grow with a Fast Pace
Glass mat thermoplastic sheets was introduced almost five decade ago. Considering the cost-related mechanical performance criteria, GMT composites are located between injection moldable, discontinues (long or short) glass-fiber-reinforced composites and advanced thermoplastic with various fiber architecture.
They offer various benefits, such as Design freedom that is production of complex parts by integrating several functions elements, low density, easy recycling, high innovation potential, in terms of production and ecological demands and high productivity. Although GMTs are available in various polymer matrices is dominated by propylene-based composites, due to their low price. These are well capable of competing with other structure materials, primarily in conditions where temperature lesser than 110°C are maintained. Glass mat thermoplastic composites are witnessing demand from the composite market. They are easy to use, with superior mechanical performance. Mercedes-Benz selected two grades of glass mat-reinforced thermoplastic material, which are supplied by the Swiss material producer, Quadrant Plastic Composites. These materials are used for manufacturing the innovative front-end module, which was designed for its S-class series luxury coupe. The new front-end module weighs only 3.4 kg, while the previous model used to weigh 5 kg.
Innovations and greater market penetration are expected to drive the demand for glass mat thermoplastic composites during the forecast period.
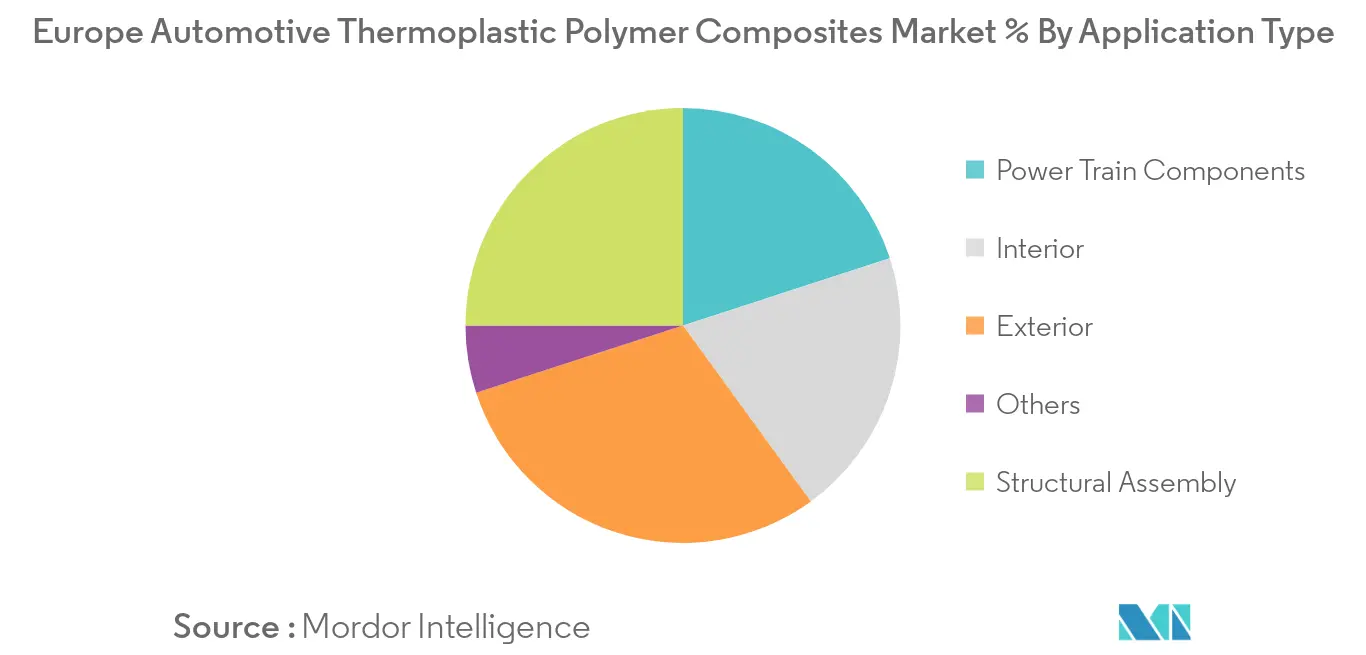
Transportation Sector to Drive the Market
The Corporate Average Fuel Economy (CAFÉ) standard forced manufacturers in the automobile industry to develop vehicle designs that incorporated high-performance light-weight materials. The weight of an automobile has a direct impact on driving dynamics, fuel consumption, and agility. A 10% reduction in vehicle weights results in approximately 5-7% rise in fuel savings. From 2020, the European Union will require every European vehicle manufacturer to achieve an emission level of 95g of carbon dioxide per km, from present-day emission level of 130g of carbon dioxide per km. The rising focus on minimizing carbon emission and enhancement of fuel economy, primarily by reducing the weight of a vehicle, are driving the demand for thermoplastics composites.
Continuous fiber-reinforced thermoplastic composites (CFRTP) is one of the primary materials that can address the rising concerns regarding a vehicle's weight. In combination with metals, CFRTP composites will be a part of a multi-material approach when designing the car of the future.
The automotive industry is undergoing a major transformation. As companies explore various options to address the future needs, collaboration has proven to be an effective way to discover the new growth avenues, will leveraging risk. The preferred approach is collaboration with strategic players throughout the value chain.
- For instance, DuPont Transportation and Advanced Polymers choose to advance through collaborative networks, while actively participating in consortia, including IACMI (Institute for Advanced Composites Manufacturing Innovation) and AZL (Aachen Centre for Integrative Lightweight Production), where standardization is addressed, along with collaborative teams that are focusing on demonstrating the production methods of cost-effective CFRTP composites, especially for high-volume applications
In 2019, SABIC announced a new, cutting-edge technology for producing lightweight, cost-effective, and recyclable vehicle panels, primarily by using its UDMAX tape, a unidirectional, fiber-reinforced thermoplastic composite, at JEC World 2019. This innovative technology, which has designed to replace traditional panels made of metal and thermoset material for interior and exterior automotive applications, will soon be commercialized in the bulkhead of a light commercial vehicle (LCV), globally.
In the case of bulkhead, replacing a traditional metal component with the UDMAX tape lamination reduces the mass by 35% in the application. Lower weight can also make large bulkhead easier to handle, which could help in accelerating the assembly process of vehicles.
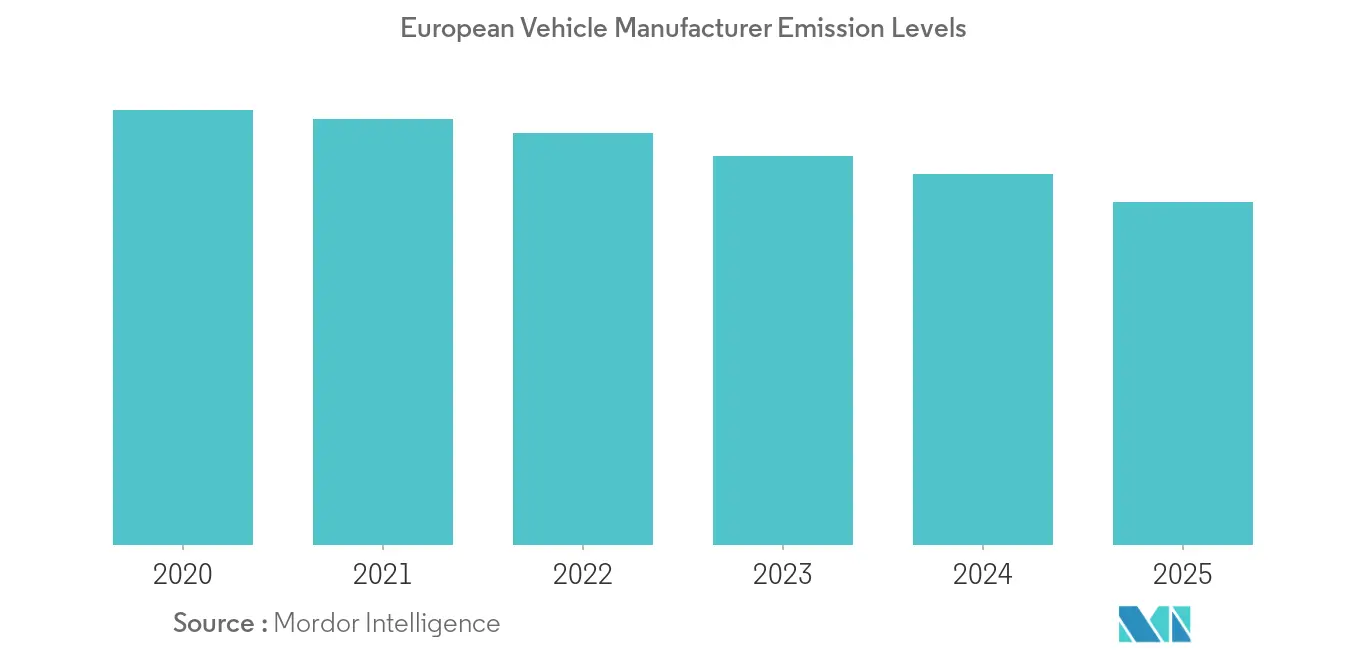