Spain Prefab Wood Buildings Market Size
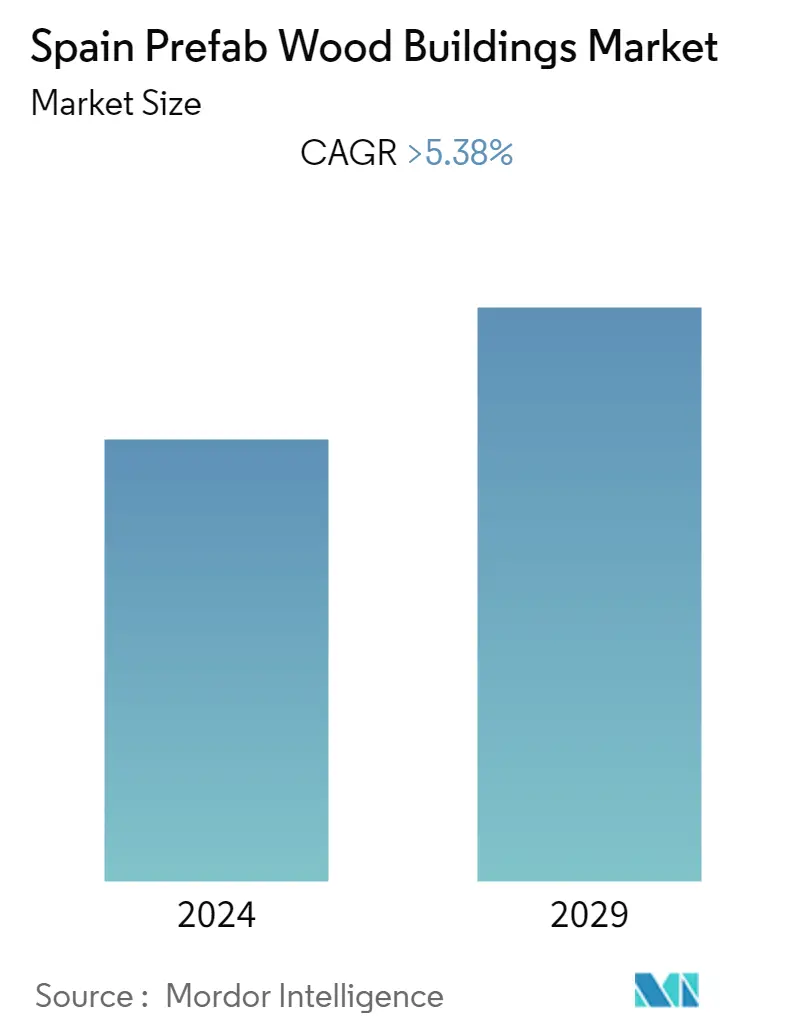
Study Period | 2020 - 2029 |
Base Year For Estimation | 2023 |
Forecast Data Period | 2024 - 2029 |
Historical Data Period | 2020 - 2022 |
CAGR | 5.38 % |
Market Concentration | Medium |
Major Players![]() *Disclaimer: Major Players sorted in no particular order |
Spain Prefab Wood Buildings Market Analysis
The size of the Spain Prefab Wood Buildings Market is USD 1.02 billion in the current year and is anticipated to register a CAGR of over 5.38% during the forecast period. The market is driven by huge investments in prefabricated buildings. Furthermore, the market is driven by the advanced technology involved.
- The government expects to invest significant sums of money to address the affordable housing situation throughout the anticipated timeframe as the housing crisis intensifies. In its 20,000 Housing Plan, the Ministry of Transport, Mobility, and Urban Agenda seek to improve the availability of public housing for low-cost rent. There are currently 642,500 floors of public housing in Spain, which makes up only 2.5% of all housing. By 2030, the government hopes to raise this to 8% with this plan. To do this, the Ministry has invested about USD 62 million, which when added to the investments made by the Autonomous Communities and City Councils, totals USD 370 million.
- Demand growth has been attributed mostly to the housing market and the construction sector. Sales of wood house frames may be hampered by the availability of popular replacements like cement and steel. In the Spanish building sector, prefabricated homes are rising in popularity. In Spain, the number of businesses that specialize in modular housing has increased dramatically in recent years, and even huge developers have started to industrialize. If prefabricated timber construction is gaining popularity, it's for good reason. Aside from wood's unique properties (low carbon footprint, possibility of local short supply chain, etc.), prefabrication now means that constructing a timber building transitions from an on-site artisanal effort to an off-site industrial production with all of the benefits that entail. Factory-made production, with less risk than on-site construction, makes it easier to control costs and save time. Because the building is built in modules in a factory, residents living near the construction site often experience less noise and pollution. Furthermore, timber waste from construction sites (renovation, demolition) has a 75% recycling and energy recovery rate.
- To thrive in a dynamic environment, you must constantly experiment and think outside the box. In recent years, there has been an increase in creative problem-solving in the field of pre-engineered buildings (PEB). The fundamental steel framework for prefabricated steel buildings is made up of built-up sections, hot-rolled sections, and cold-formed components, while the roof and wall cladding are made up of single skin sheeting with extra insulation or insulated sandwich panels, respectively. These Pre-Engineered Steel Buildings' structural components can be customised to meet a variety of requirements. It has many advantages over more traditional structures for any low-rise construction. The various submarkets that comprise the international prefabricated building industry are defined by regional, structural, and functional specialisations.
Spain Prefab Wood Buildings Market Trends
This section covers the major market trends shaping the Spain Prefab Wood Buildings Market according to our research experts:
Rising benefits of wood fabrication has driven the market
Spain's prefab industry is anticipated to expand during the projection period as a result of the government's emphasis on the nation's infrastructure. Over the coming years, expanded road and rail infrastructure is anticipated to enable continued growth in the modular and prefab construction sector. Numerous advantages of prefabricating wood include process efficiency, a regulated environment, a higher return on investment, material efficiency, decreased on- and off-site waste, and sustainability.
All of these advantages contribute to meeting the requests for improved buildings made by owners, architects, and tenants. At every level, from design to production to building, process efficiency is a possibility. Planning in great detail enables building procedures to be standardized and optimized, resulting in construction efficiency that adheres to strict deadlines and cuts down on on-site assembly time. Prefabricated parts are sorted and placed onto trucks in order to reduce on-site handling, which improves sequencing. The procedure is also better integrated, which improves communication between the parties and cuts down on expensive change orders.
Because prefabricated components are made in a controlled atmosphere, they are more precise and of higher quality. Additionally, fabrication efficiency is increased, tradespeople's safety is improved, and the construction process is not slowed down by weather. Due to layoffs and other budgetary constraints, Waste in terms of resources and time is minimised. Despite the fact that building components are frequently more expensive up front, on-site construction is typically kept to a minimum, which lowers the overall installation cost.
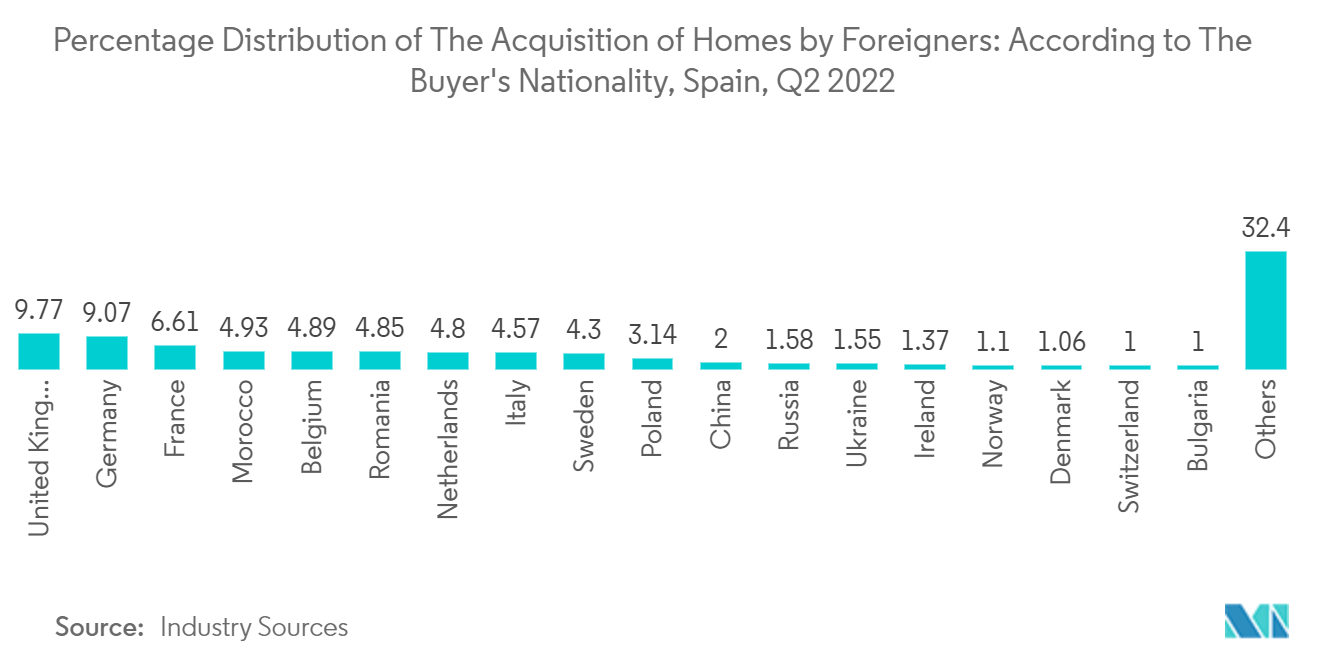
Increasing Adoption of Wood Housing in Construction Sector
Prefabricated components are produced off-site and often using modelling technologies that offer extremely precise measurements, which leads to material efficiency. Because components are created or cut to precise measurements and have predetermined sizes and dimensions, there is less trash generated both on and off-site, reducing the project's impact on the environment. This refers to the sustainability of prefabrication as well. Buildings' effects on the environment must be quantified throughout their whole existence, from design through facilities management.
Prefab construction gives architects and building industry experts more control over how structures are made, allowing them to choose more environmentally friendly building materials and techniques while also improving their ability to forecast future energy efficiency. Prefabrication is a technique that can be used to improve the sustainability of construction from the viewpoint of a facility's entire lifecycle, particularly considering demolition or reuse, as the case may be. Future entire lifetime sustainability may benefit most from prefabrication's ability to produce structures that adapt to time, change, and reuse/recycle materials.
The popularity of prefabricated homes is rising in the architectural community. Either due to teleworking, which makes it simpler to live outside of the city, or because it is now nearly difficult to rent or own what were formerly typical flats or homes due to the high cost of the property. According to data from various Building platforms, the demand for prefabricated and manufactured homes has increased between 30% and 60% in Spain. As a result, consumers have a wider range of alternatives and choices. Prefabricated homes are becoming more popular, though they haven't yet taken off in Spain as they have in other nations.
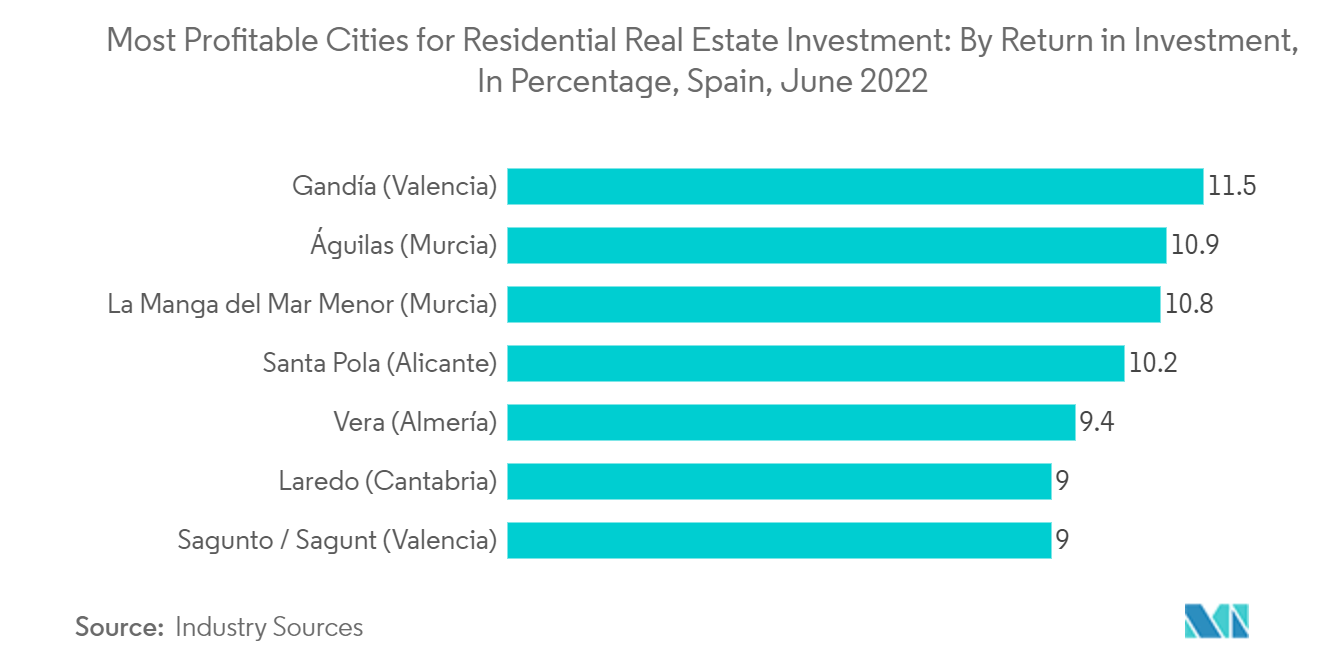
Spain Prefab Wood Buildings Industry Overview
The Spain Prefab Wood Buildings Market is partially fragmented, but it is likely to grow during the forecast period as prefab construction building investments and upcoming significant projects in various developing and developed countries increase. The major players include Tokamadera Estructuras Modulares S.l., Cabisuar SA., Casas De Madera Caminas, Viprehome., Balat, and Canval Empresa Constructora, S.L.With an increase in product expansions, technical advances, and M&A, competition is projected to heat up significantly more.
Spain Prefab Wood Buildings Market Leaders
-
Tokamadera Estructuras Modulares S.l
-
Cabisuar SA
-
Viprehome
-
Balat
-
Canval Empresa Constructora, S.L
*Disclaimer: Major Players sorted in no particular order
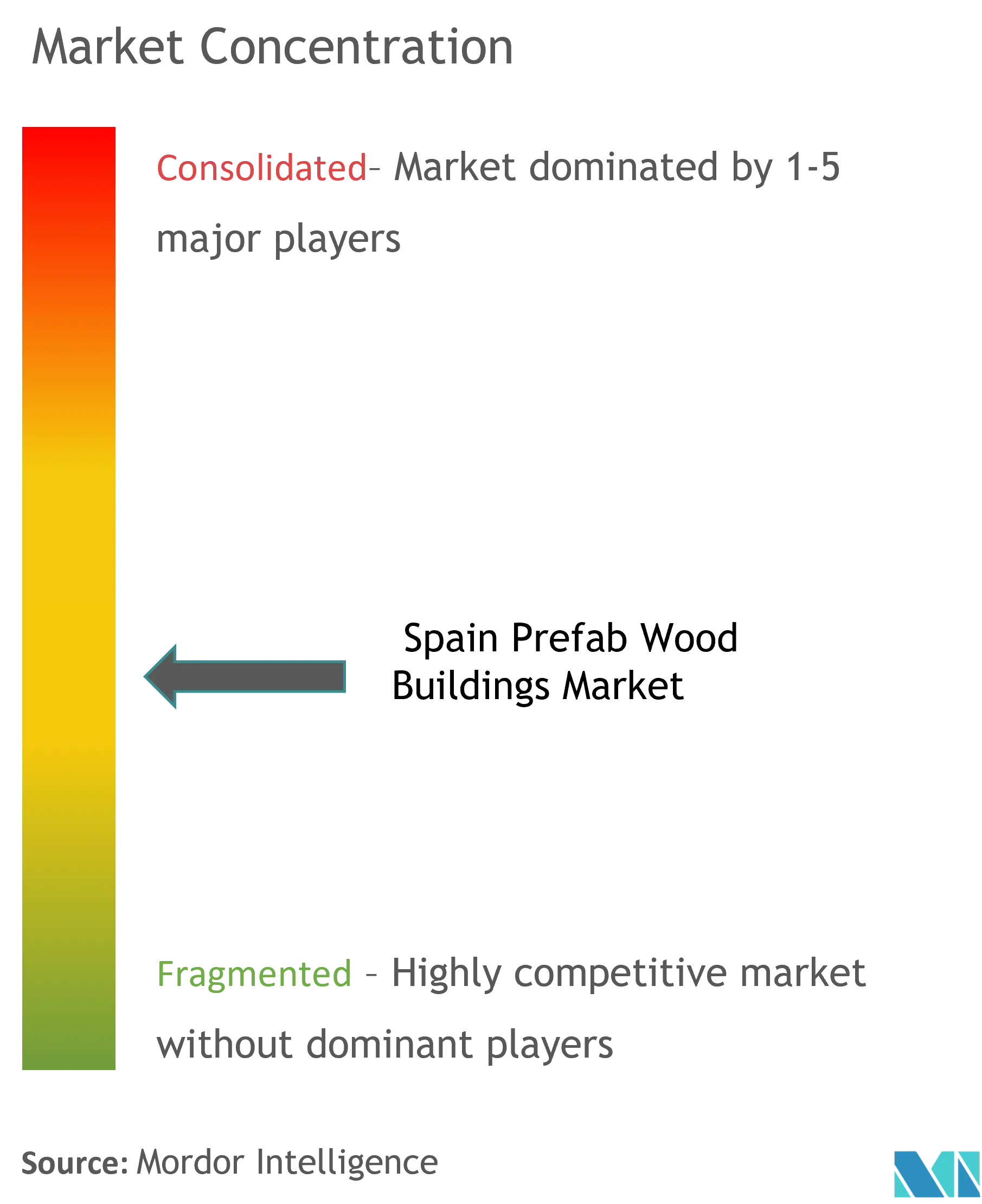
Spain Prefab Wood Buildings Market News
- February 2022- Spanish studio Peris+Toral Arquitectes has completed an 85-unit social housing project in Barcelona, featuring a modular timber framework and flexible living spaces. According to the studio, the project is the largest wooden-structured residential building in Spain, built from 8,300 cubic metres of timber harvested from the forests of the Basque Country.
- February 2022- The ON-A studio, from Barcelona, has collaborated with the company Energreen Design, which specialized in sustainability, energy efficiency and circular economy applied to construction, to create a prefabricated house of modular construction. Green Nest House is a wooden house that blends in with nature and has revolutionized the sustainable real estate market. The construction company in charge of carrying out the project was WES.
Spain Prefab Wood Buildings Market Report - Table of Contents
1. INTRODUCTION
- 1.1 Market Definition and Scope
- 1.2 Study Assumptions
2. RESEARCH METHODOLOGY
3. EXECUTIVE SUMMARY
4. MARKET DYNAMICS AND INSIGHTS
- 4.1 Market Overview
- 4.2 Market Drivers
- 4.3 Opportunities
- 4.4 Value Chain / Supply Chain Analysis
-
4.5 Industry Attractiveness - Porter's Five Force Analysis
- 4.5.1 Threat of New Entrants
- 4.5.2 Bargaining Power of Buyers/Consumers
- 4.5.3 Bargaining Power of Suppliers
- 4.5.4 Threat of Substitute Products
- 4.5.5 Intensity of Competitive Rivalry
- 4.6 Government Regulations and Initiatives
- 4.7 Technological Trends
- 4.8 Brief on Different Structures Used in the Prefabricated Buildings Industry
- 4.9 Cost Structure Analysis of the Prefabricated Buildings Industry
- 4.10 Impact of COVID-19 on the Market
5. MARKET SEGMENTATION
-
5.1 Panel Systems
- 5.1.1 Cross-laminated timber (CLT) panels
- 5.1.2 Nail-laminated timber (NLT) panels
- 5.1.3 Dowel-laminated timber (DLT) panels
- 5.1.4 Glue-laminated timber (GLT) columns and beams
-
5.2 Application
- 5.2.1 Single Family Residential
- 5.2.2 Multi-family Residential
- 5.2.3 Office
- 5.2.4 Hospitality
- 5.2.5 Others
6. COMPETITIVE LANDSCAPE
- 6.1 Market Concentration Overview
-
6.2 Company Profiles
- 6.2.1 Tokamadera Estructuras Modulares S.l
- 6.2.2 Cabisuar SA
- 6.2.3 Casas De Madera Caminas
- 6.2.4 Viprehome
- 6.2.5 Balat
- 6.2.6 Canval Empresa Constructora, S.L.
- 6.2.7 Sismoha
- 6.2.8 Casas Tecnohome
- 6.2.9 Mundocasetas
- 6.2.10 Casas Natura*
- *List Not Exhaustive
7. FUTURE OF SPAIN PREFAB WOOD BUILDINGS MARKET
8. APPENDIX
** Subject To AvailablitySpain Prefab Wood Buildings Industry Segmentation
Prefabricated wood construction kits, similar to life-sized Legos, are constructed out of prefabricated components that are supplied and installed on-site. This is most commonly accomplished by the use of prefabricated panels that may create complete portions of a building, such as roofing components or structure (ceiling, decking, and beams), building structure (wall panels, beams, columns, and shear panelling), and even glazing packages. A complete background analysis of the Spain Prefab Wood Buildings Market, including the assessment of the economy and contribution of sectors in the economy, market overview, market size estimation for key segments, and emerging trends in the market segments, market dynamics, and geographical trends, and COVID-19 impact is included in the report.
The Spain Prefab Wood Buildings Market is segmented By Panel Systems (Cross-laminated timber (CLT) panels, Nail-laminated timber (NLT) panels, Dowel-laminated timber (DLT) panels, and Glue-laminated timber (GLT) columns and beams), and By Application (Single Family Residential, Multi-family Residential, Office, and Hospitality). The report offers market size and forecasts in value (USD billion) for all the above segments.
Panel Systems | Cross-laminated timber (CLT) panels |
Nail-laminated timber (NLT) panels | |
Dowel-laminated timber (DLT) panels | |
Glue-laminated timber (GLT) columns and beams | |
Application | Single Family Residential |
Multi-family Residential | |
Office | |
Hospitality | |
Others |
Spain Prefab Wood Buildings Market Research FAQs
What is the current Spain Prefab Wood Buildings Market size?
The Spain Prefab Wood Buildings Market is projected to register a CAGR of greater than 5.38% during the forecast period (2024-2029)
Who are the key players in Spain Prefab Wood Buildings Market?
Tokamadera Estructuras Modulares S.l, Cabisuar SA, Viprehome, Balat and Canval Empresa Constructora, S.L are the major companies operating in the Spain Prefab Wood Buildings Market.
What years does this Spain Prefab Wood Buildings Market cover?
The report covers the Spain Prefab Wood Buildings Market historical market size for years: 2020, 2021, 2022 and 2023. The report also forecasts the Spain Prefab Wood Buildings Market size for years: 2024, 2025, 2026, 2027, 2028 and 2029.
Spain Prefab Wood Buildings Industry Report
Statistics for the 2024 Spain Prefab Wood Buildings market share, size and revenue growth rate, created by Mordor Intelligence™ Industry Reports. Spain Prefab Wood Buildings analysis includes a market forecast outlook to (2024to2029 and historical overview. Get a sample of this industry analysis as a free report PDF download.