Market Size of Global Spark Plasma Sintering Industry
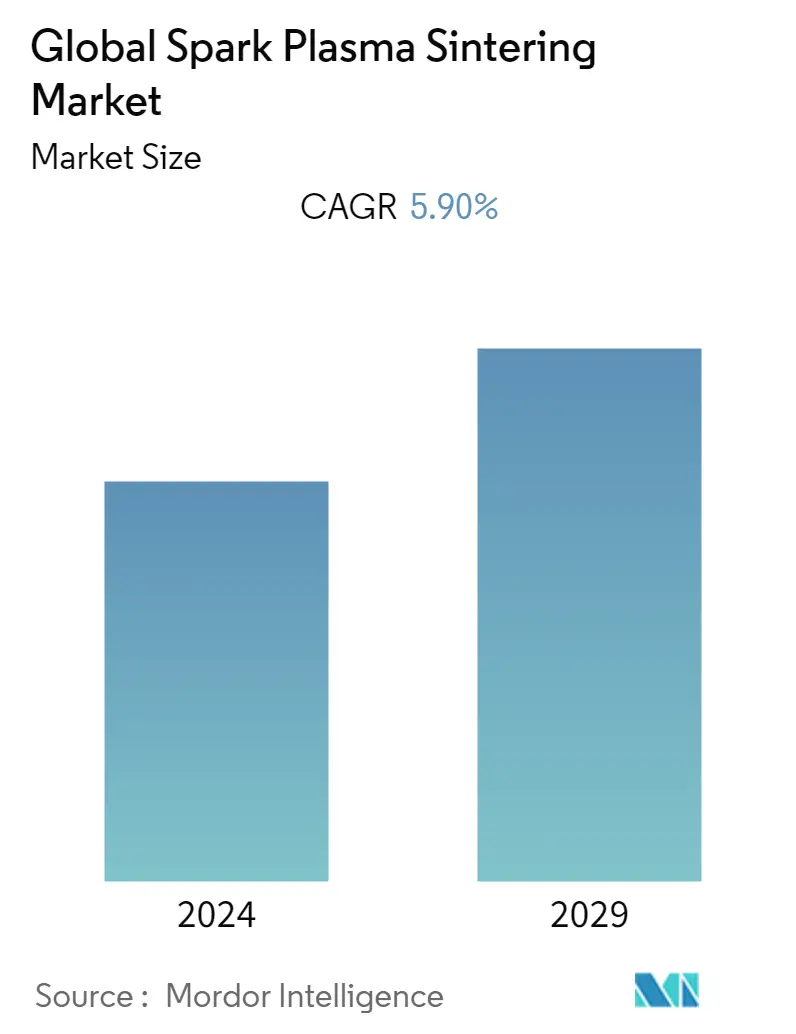
Study Period | 2019 - 2029 |
Base Year For Estimation | 2023 |
CAGR | 5.90 % |
Fastest Growing Market | North America |
Largest Market | North America |
Market Concentration | High |
Major Players![]() *Disclaimer: Major Players sorted in no particular order |
Spark Plasma Sintering Market Analysis
The Spark Plasma Sintering Market is projected to register a CAGR of over 5.9% during the forecast period. The rising adoption of the electric current-assisted sintering method as a tool for the consolidation of various metallic/non-metallic powders and the increasing adoption of the field-assisted sintering technique (FAST) for designing nanomaterials are some of the significant growth drivers for the studied market.
- In the last couple of decades, elaboration techniques based on high current intensities have attracted substantial interest from industrial sectors. Among these techniques, spark plasma sintering has emerged as the most adopted method in the last few years. The SPS technique has recently made significant advancements in materials science and materials processing due to the capability of fast and efficient densification of various materials and the suitability of the equipment for conducting solid-state syntheses and syntheses.
- SPS, also known as FAST, is a high-speed powder consolidation technology that develops quality-centered products from nanomaterials. The technology has gained significant attention for its ability to retain nanocrystalline microstructures and create materials with interesting functional properties. SPS systems have surpassed conventional methods, like hot press (HP) sintering, hot isostatic pressing (HIP), or atmospheric furnaces. Micro-spark/plasma is the most common technique among various proposed physical mechanisms for the SPS process.
- In recent years, SPS has emerged as the preferred option for producing high-strength, ultra-fine crystalline materials; dispersion strengthened materials, thermoelectric or metal-diamond (or generally metal-carbon) composite materials, and sputter targets. Besides, the process facilitates the adjustment of temperature gradients within the sintering body during compaction. It enables the production of gradient and layered materials with widely differing properties (e.g., ZrO2/stainless steel, Al2O3/titanium).
- The increasing adoption of the SPS method as a tool for consolidating powders is also demonstrated by a large number of papers published in recent years. Although SPS is still an emerging technology, slow developments, research, and applications have been increasingly witnessed in recent years, attracting great attention from the research and industrial sectors. For instance, one of the most common applications of SPS is the sintering of high melting point materials, such as titanium nitride. They have been extensively used in the aerospace industry for compressor, turbine, and pressure piping in an engine, owing to their high corrosion resistance, high strength, and relatively lightweight. These factors are fuelling their deployment in the automotive and defense sector.
- Some of the industrial applications of SPS include fuel cell materials, high strength and wear-resistant tooling, sputter targets, diamond compaction for abrasives, and the development of pure or mixed metallics, ceramics, or cermets, where maintaining nanometric and fine microstructure is required. The increasing adoption of innovative metals, composite materials in industrial and consumer products, and ceramics is anticipated to grow during the forecast period, owing to their increasing availability and decreasing manufacturing costs.
- Moreover, during the COVID-19 lockdown, many types of research were carried out in the SPS, which had a positive influence on the studied market growth. For instance, in April 2021, IDAHO researchers will help the industry make high-performance parts inexpensive and durable. Idaho National Laboratory developed advanced capabilities to help the industry design efficient SPS manufacturing processes. The lab's latest addition, one of the largest machines of its kind worldwide, makes it possible to manufacture new materials at industrially relevant scales. INL designed and built four custom SPS machines that range from supporting small experiments on the bench scale to industrial-scale, large-format, and high-throughput systems.
- However, SPS requires a significant up-front investment in time and expense. The operational variables include but are not limited to heat ramp rates, material properties, die design and material, hold temperatures and times, force strategies, vacuum, atmospheric conditions, power settings, and cooling conditions. This can act as a restraining factor to the growth of the market.
Spark Plasma Sintering Industry Segmentation
The spark plasma sintering (SPS) is also known as Field Assisted Sintering Technique (FAST). The process uses a high electrical current to rapidly heat a conductive tooling assembly under simultaneous uniaxial pressure inside a vacuum chamber. With no heating elements, extremely rapid heating and cooling of the sample is possible, enabling high-density materials to be sintered with ultra-fine or even nano-sized grain structures. It is one of the sintering approaches to processing biomaterials in the laboratory.
The Global Spark Plasma Sintering Market is segmented By End-user Applications (Automotive, Manufacturing, Energy & Power, Aerospace & Defense) and Geography.
By End-user Application | |
Automotive | |
Manufacturing | |
Energy & Power | |
Aerospace & Defense | |
Other End-user Applications |
By Geography | |
North America | |
Europe | |
Asia Pacific | |
Latin America | |
Middle East and Africa |
Global Spark Plasma Sintering Market Size Summary
The Spark Plasma Sintering (SPS) market is experiencing significant growth, driven by its increasing adoption in various industrial sectors. This high-speed powder consolidation technology, also known as Field-Assisted Sintering Technique (FAST), is gaining traction due to its ability to efficiently densify materials and retain nanocrystalline microstructures. SPS has surpassed traditional methods like hot press sintering and hot isostatic pressing, offering advantages in producing high-strength, ultra-fine crystalline materials and composite materials with unique functional properties. The technology's application in sectors such as aerospace, automotive, and defense is expanding, particularly for high melting point materials like titanium nitride, which are valued for their corrosion resistance and strength. The automotive industry, especially the electric vehicle sector, presents lucrative opportunities for SPS, as it is used in developing thermoelectric generators that convert waste heat into electricity.
The Asia-Pacific region is a major adopter of SPS systems, driven by its robust manufacturing sector, particularly in electronics and semiconductors. The region's growing medical tourism industry and increasing defense spending further bolster the demand for SPS technologies. The market is characterized by a consolidated landscape with key players like Thermal Technology LLC leading the industry. Despite the high capital investment and expertise required for SPS technology, advancements and research during the COVID-19 pandemic have positively influenced market growth. Innovations such as integrated touch screen controls and data storage solutions are enhancing SPS systems' appeal. The market's expansion is supported by strategic investments, such as Safran Corporate Ventures' funding in the French startup Sintermat, highlighting the ongoing interest and potential for growth in the SPS market.
Global Spark Plasma Sintering Market Size - Table of Contents
-
1. MARKET DYNAMICS
-
1.1 Market Drivers
-
1.1.1 Increase in Defense Budgets Across Geographies
-
-
1.2 Market Restraints
-
1.2.1 Highly Consolidated Market
-
-
-
2. MARKET SEGMENTATION
-
2.1 By End-user Application
-
2.1.1 Automotive
-
2.1.2 Manufacturing
-
2.1.3 Energy & Power
-
2.1.4 Aerospace & Defense
-
2.1.5 Other End-user Applications
-
-
2.2 By Geography
-
2.2.1 North America
-
2.2.2 Europe
-
2.2.3 Asia Pacific
-
2.2.4 Latin America
-
2.2.5 Middle East and Africa
-
-
Global Spark Plasma Sintering Market Size FAQs
What is the current Global Spark Plasma Sintering Market size?
The Global Spark Plasma Sintering Market is projected to register a CAGR of 5.90% during the forecast period (2024-2029)
Who are the key players in Global Spark Plasma Sintering Market?
Fuji Electronic Industrial Co. Ltd., Dr Fritsch GmbH & Co KG, Thermal Technology LLC, FCT Systeme GmbH and MTI Corporation are the major companies operating in the Global Spark Plasma Sintering Market.